How We Produce?
At our company, the production of our textile products is a harmonious blend of traditional craftsmanship and cutting-edge technology. We take pride in every step of the process, from the selection of materials to the final presentation of our exquisite garments. Here's a glimpse into how we bring our vision to life:
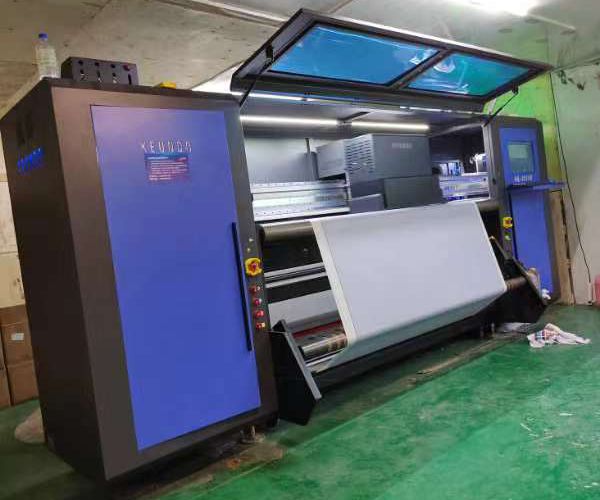
Print on Paper
Print on paper is the traditional method of printing where designs are transferred onto paper substrates. With the advent of digital technologies, printing on paper has seen a significant transformation. From brochures to posters, the quality and speed of output have improved dramatically. Key features include:
- Precision: High-resolution printing ensures crisp text and vivid imagery.
- Range: Suitable for a variety of paper types and finishes.
- Cost-effective: Ideal for large-volume print runs.
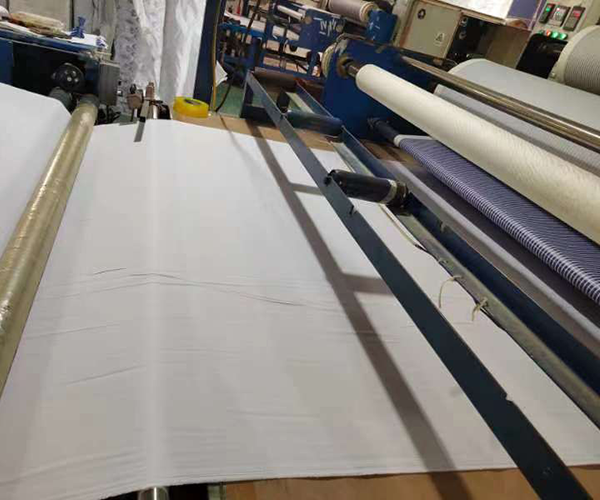
Print on Fabric
Print on fabric technology enables direct printing onto textile materials. Utilizing advanced digital inkjet printers, this method allows for vibrant, high-resolution patterns and designs to be transferred directly onto fabrics, from cotton to silk and synthetics. The advantages include:
- Versatility: Capable of reproducing intricate designs with multiple colors.
- Flexibility: Ideal for small batches or one-off designs without the need for screens or plates.
- Eco-friendly: Uses water-based inks, reducing environmental impact.
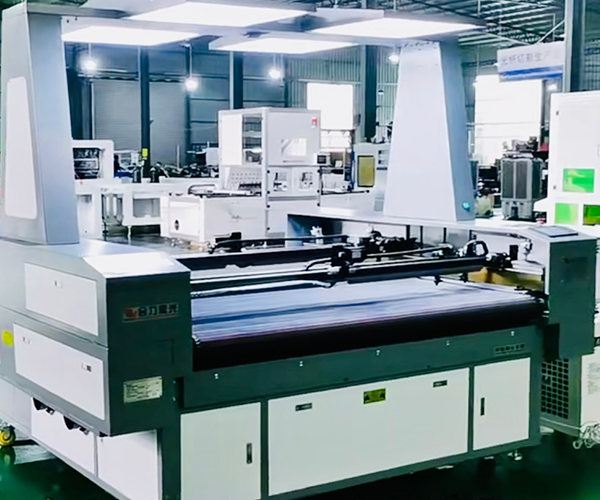
Lazer Cut
Laser cutting is a technology that uses a high-power laser beam to cut or engrave materials. Controlled by computer software, the laser beam vaporizes, burns, or melts the material, resulting in precise cuts or engravings. While commonly associated with metals, laser cutting can also be used on textiles, plastics, wood, and more. Benefits of this technology are:
- Precision: Offers intricate cuts with extreme accuracy.
- Clean Edges: The cutting process results in smooth, clean edges without fraying.
- Versatility: Can be used on a wide range of materials and for various applications from fashion to industrial components.
- Minimal Waste: Laser cutting is precise, leading to reduced material waste.
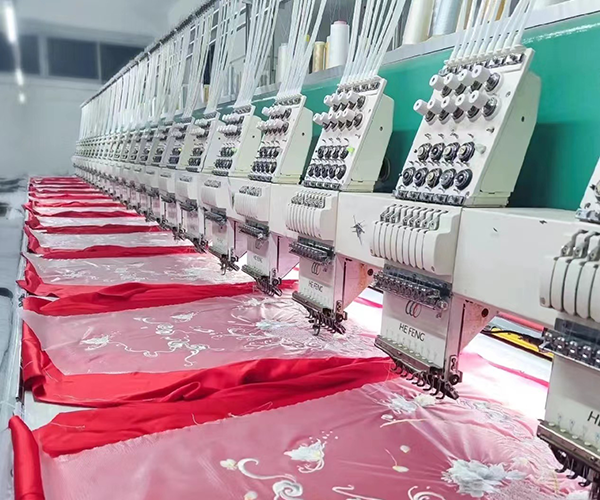
Embriodering
Embroidering, a timeless art form that dates back centuries, has been enhanced and revolutionized by modern technology, making it a blend of tradition and innovation.
- Machine Embroidery: Modern embroidering machines, controlled by computer systems, can produce intricate designs with precision and consistency at a much faster pace than hand embroidery. These machines can handle multiple colors and stitch types simultaneously.
- Digital Design Integration: Today's embroidery benefits from digital design software. Artists and designers can create or modify a design digitally, and then this design is translated into stitch instructions for embroidery machines.
- Materials & Threads: Advanced materials and specialized threads, including metallic, variegated, and even UV-reactive, allow for diverse aesthetic and functional applications. This means embroidery can be more durable, vibrant, and even interactive.
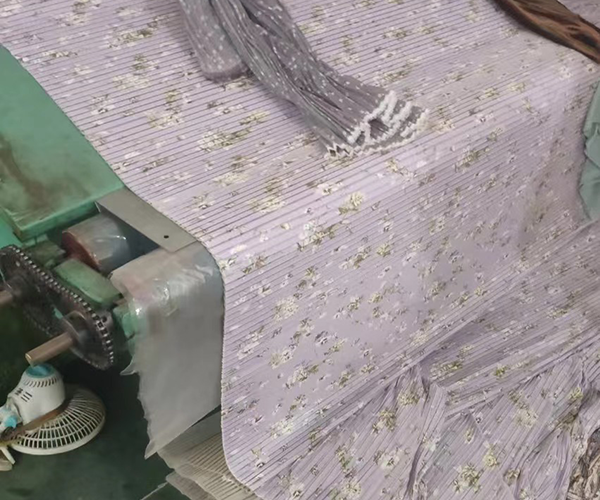
Pleating
Pleating, the art of folding fabric in a repeated pattern, has been an integral part of fashion and textile arts for centuries. Modern technology has refined and expanded the capabilities of this age-old technique, enabling a wide variety of precise and consistent pleats.
- Machine Pleating: Unlike the traditional hand-folded method, machine pleating uses specialized equipment to fold fabrics uniformly. Machines can be set to create different pleat sizes and patterns, resulting in consistent and high-speed production.
- Digital Design and Control: Modern pleating machines often come with digital interfaces that allow designers to program and control the size, spacing, and pattern of pleats. This digital precision ensures that the desired design is flawlessly executed.
- Heat-set Pleating: Certain synthetic fabrics can retain pleats when exposed to heat. The fabric is pleated and then passed through a controlled heating process, ensuring the pleats are 'set' and remain intact for a prolonged period.
- Crystal Pleating: One of the smallest and finest types of pleats, crystal pleating is achieved using advanced machinery to create tight, close-together pleats.
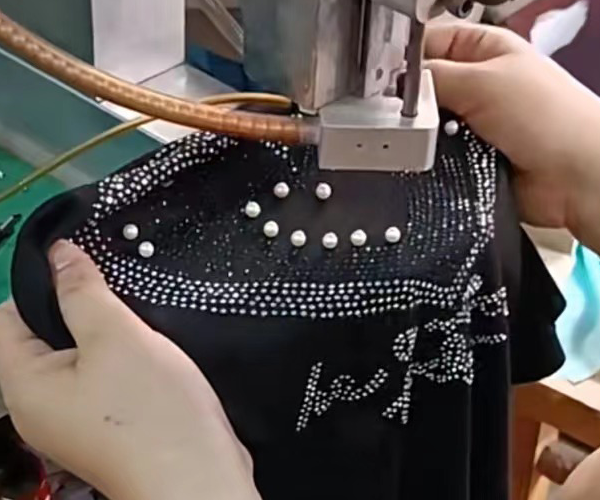
Glue-on & Hotfix Rhinestone
Rhinestones, often used to adorn clothing, accessories, and various other items, can be applied through several techniques. Among these, the "glue-on" and "hotfix" techniques are prominent in Chinese garment decoration.
Glue-on Rhinestones
- Precision: The placement can be precise, allowing for intricate designs and patterns.
- Versatility: This method is suitable for a wide variety of materials, including those that might not withstand heat.
- Durability: Once the adhesive is cured, the rhinestones are securely attached, though they might be less durable than heat-set rhinestones under heavy wear or frequent washing.
Hotfix Rhinestones
- Efficiency: This method allows for quicker application, especially with the use of specialized tools or machines.
- Durability: Heat-set rhinestones tend to have a strong bond, making them durable and resistant to washing and wear.
- Special Equipment: Using a heat press or a hotfix applicator tool ensures even heat distribution and optimal adhesion.